It’s Construction Safety Week.
Across the U.S., leaders in the industry are hosting stand-downs, conducting toolbox talks and ramping up training as a means of highlighting best practices and ensuring each worker on the jobsite gets home safely.
If you ask the environmental, health and safety chiefs working for major players in construction, they’ll tell you safety is not a competition. Sharing practices and collaborating on events like Safety Week is part of how the industry improves the overall well-being of the workforce.
Here, leaders share their best practices with Construction Dive for making a difference in worker safety and health. Read on to see the programs they’re proudest of.
The following responses have been edited for brevity and clarity.
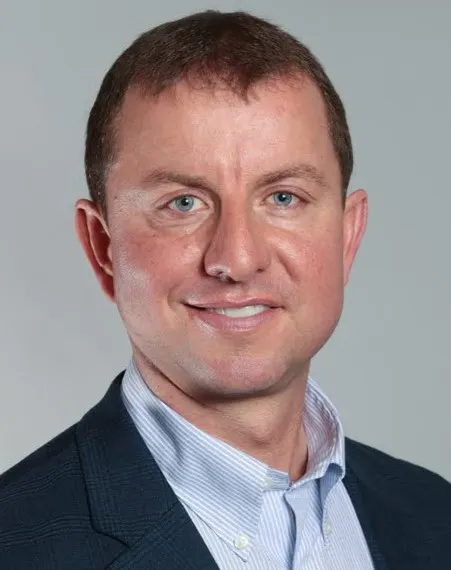
Dave Hulverson
Permission granted by Granite Construction
Dave Hulverson, Granite Construction senior vice president of safety, health, environment and quality: The most significant safety practice we have enacted in the past several years is our STCKY initiative. STCKY stands for “Stuff that can kill you,” and is a training enhancement that teaches our workers about the riskiest high-energy hazards on construction sites and how to recognize and mitigate those hazards. This initiative has been a game-changer in improving worker safety and health.
In addition, we recently implemented the Granite Guard hand safety initiative to standardize our hand and power tools across the company. This has helped reduce the more common though less severe injuries so we can spend more time focused on eliminating STCKY.
Tricia Thibodeaux, Fluor vice president of health, safety and environmental: Certain construction operations exhibit a disproportionately high number of precursors for fatalities or serious injuries. After evaluating industry data and our own incident history, Fluor identified nine operations conducted widely across the company that present the greatest risk of a fatality or serious injury.
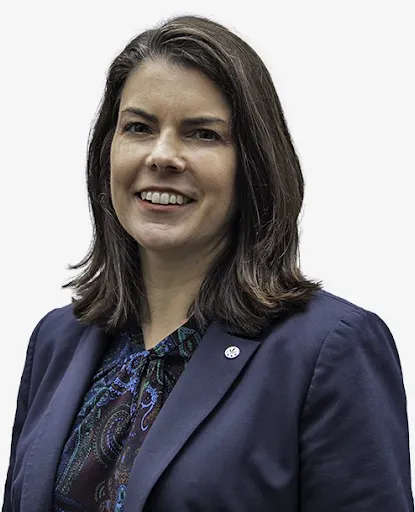
Tricia Thibodeaux
Permission granted by Fluor
Subject matter experts from across the organization collaborated to enhance work practices, training, and risk assessments for what we call the Life Critical operations.
Fluor developed the Safer Choices Together program to educate workers about their personal risk tolerance and its impact on decision-making. This initiative underscores the importance of making safer choices and recognizing potential hazards before they become issues.
Given the multitude of decisions made daily, each with the potential for error, effective decision-making is crucial to maintaining our Safer Together culture. Individuals must choose to work safely, and their safe choices are facilitated by both personal and management engagement.
Safer Choices Together emphasizes individual learning, self-awareness, personal investment and growth, and input from the work front, empowering construction professionals to make informed and safe decisions.
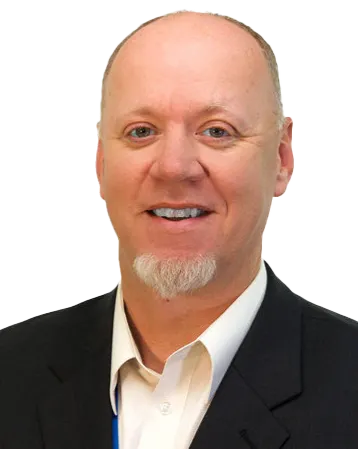
Lonnie Schock
Permission granted by DPR
Lonnie Schock, DPR environmental health and safety and leadership team member: Like others in the construction industry, we have come to recognize that the things that cause high-frequency injuries, like hand and soft tissue injuries, are not the same things that cause severe, high-impact incidents. With that context, DPR has expanded our safety focus to be more all-encompassing and to equip our teams with the right tools and resources to better anticipate risks, so they can be effectively managed and thus keep people safe.
As part of this, we have started exploring the use of new, emerging technologies like machine learning and AI, to analyze data and predict potential jobsite hazards so that we can more effectively and proactively act before something goes wrong.
Todd Friis, Clayco senior vice president of risk management: We rely a lot on our data to inform the path we take with our safety program. For example, we see that a lot of injuries happen earlier in the day, so we have placed an emphasis on “The Golden Hour.” It’s that time, first thing in the morning where our field supervisors spend a lot more time out of the office and in the field.
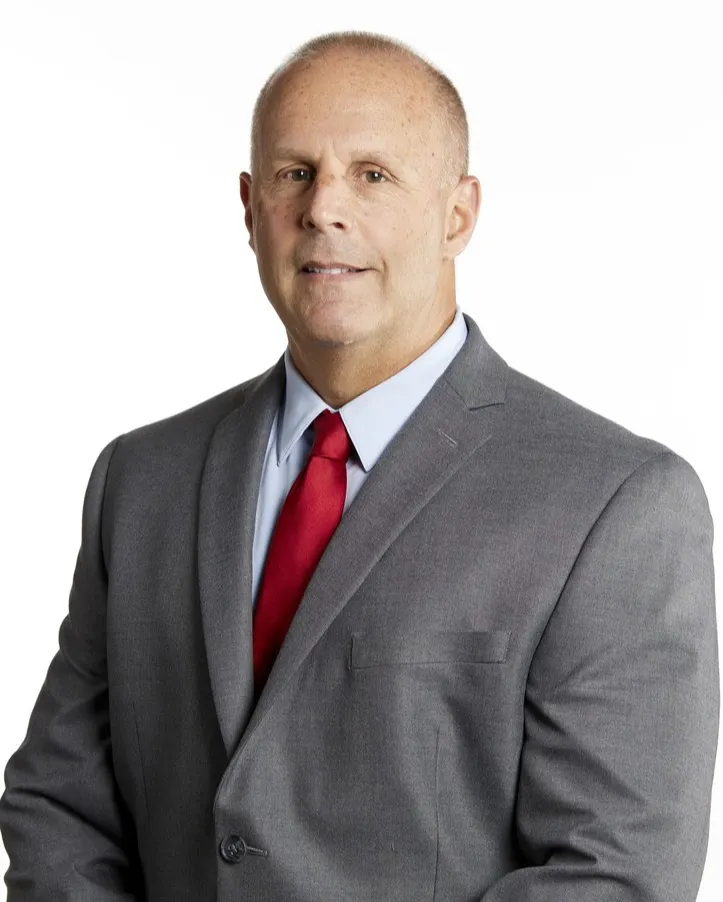
Todd Friis
Permission granted by Clayco
Over the years, we have seen more and more workers who are brand new to the construction workforce that do not have a lot of understanding of construction safety. Looking forward, we are trying to help boost this knowledge among our subcontractors by requiring all workers to have at least an OSHA 10 construction certification when they work on our jobsites.
While this requirement technically doesn’t go into effect until July 1 of this year, we are already working with our trade partners to help their workers complete this training now. It is our feeling that making this a part of our process will help increase awareness and knowledge of safety, not just on Clayco jobsites, but as they move out to work for other contractors as well, helping to improve safety in some way across the industry.
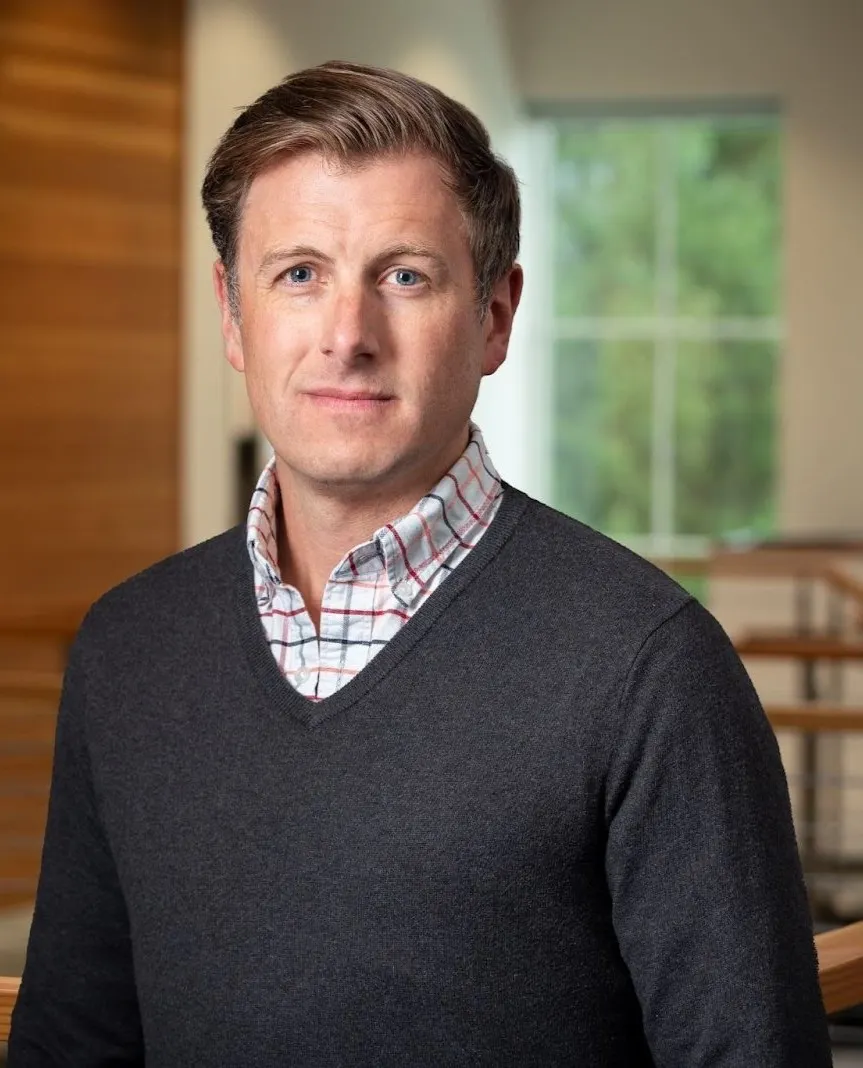
Bryan Kingsbury
Permission granted by Consigli
Bryan Kingsbury, Consigli Construction corporate safety director: Beyond making basic upgrades or enhancements to PPE or equipment, such as requiring helmets with chin strap retention, we’ve also identified opportunities where we can leverage our in-house Virtual Design & Construction team to create safer, more sustainable jobsites. As technology and AI continues to develop, we’ve been intentional about staying innovative in our approach to safety so that we can stay ahead of the curve and make sure our teams are equipped with state-of-the-art resources.
Using drones flown by our VDC team, we can conduct virtual safety walks for high-reach and higher-risk areas, like roofs and site perimeters, which allows us to inspect and improve areas that aren’t easily accessible. We’re also using a new AI tool to analyze images taken of our jobsites, identify safety hazards and make corrective recommendations in an efficient and effective way. With AI and cutting-edge VDC solutions, issues with site access, PPE, material storage and more can all be quickly identified — and resolved — by Consigli teams..
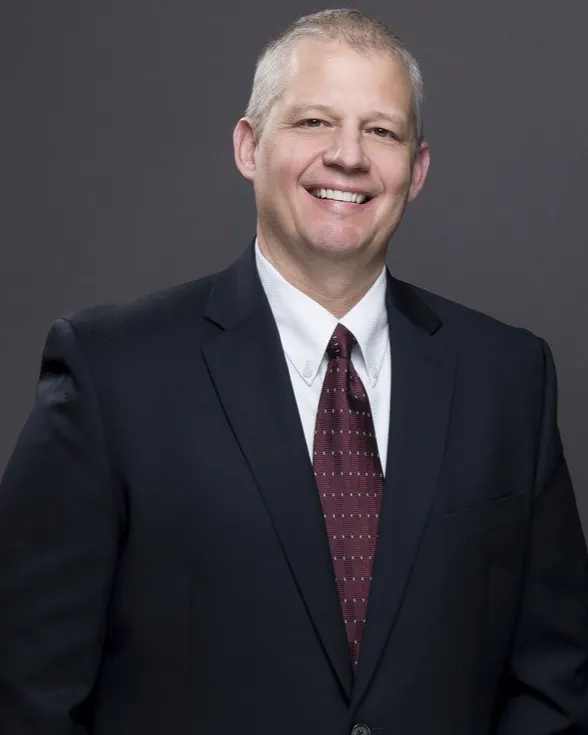
Jeff Palombo
Permission granted by Robins & Morton
Jeff Palombo, Robins & Morton vice president of safety operations: Our approach to safety management is grounded in our human performance operating philosophy, which acknowledges the complexity of our operating system and its influence on behavior, including human error. We understand that errors expose system weaknesses, not personal failings, and blame does not improve performance — fixing the process does.
By emphasizing that workers are not the problem, and are instead part of the solution, a project’s leadership, culture, safety system design and defenses can truly thrive and succeed.
To support this approach, we have developed tools, defenses and consequence control strategies that provide our workforce with the capability and flexibility to safely perform work in an ever-evolving environment. Those include:
- Task planning meetings.
- Post-task reviews.
- Performance coaching.
- Granting team members stop-work authority.
- Team forums.